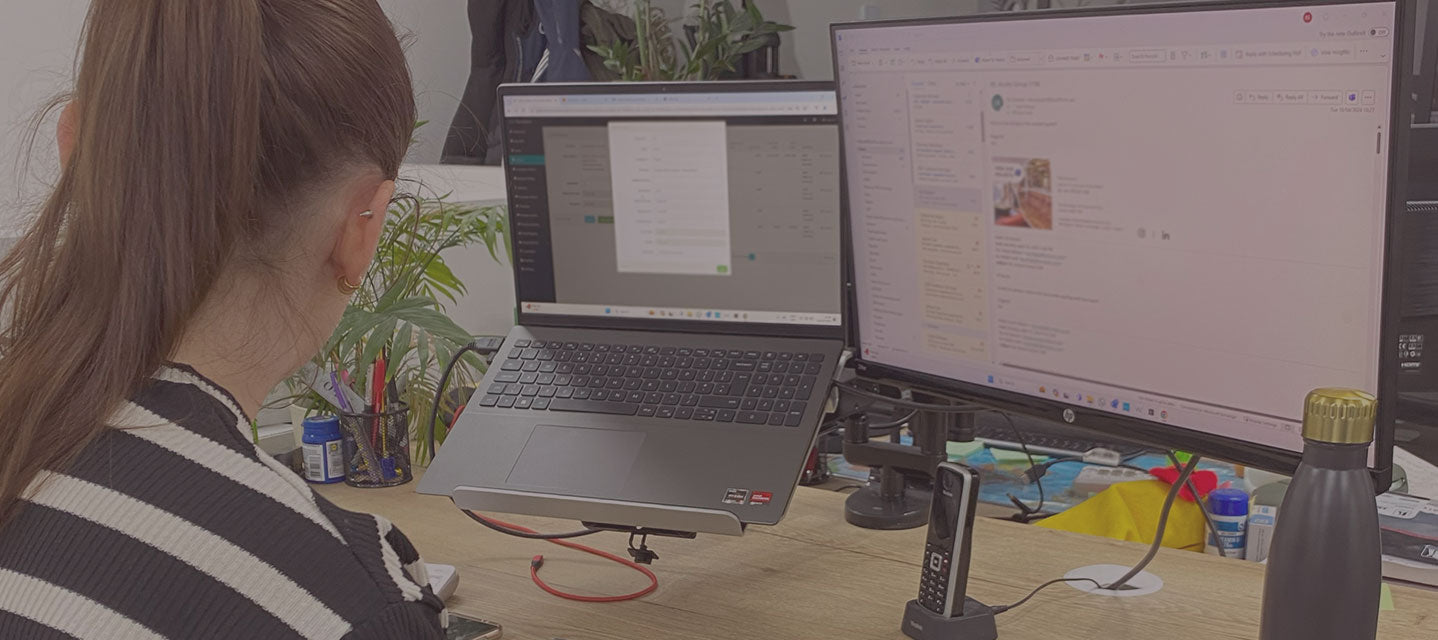
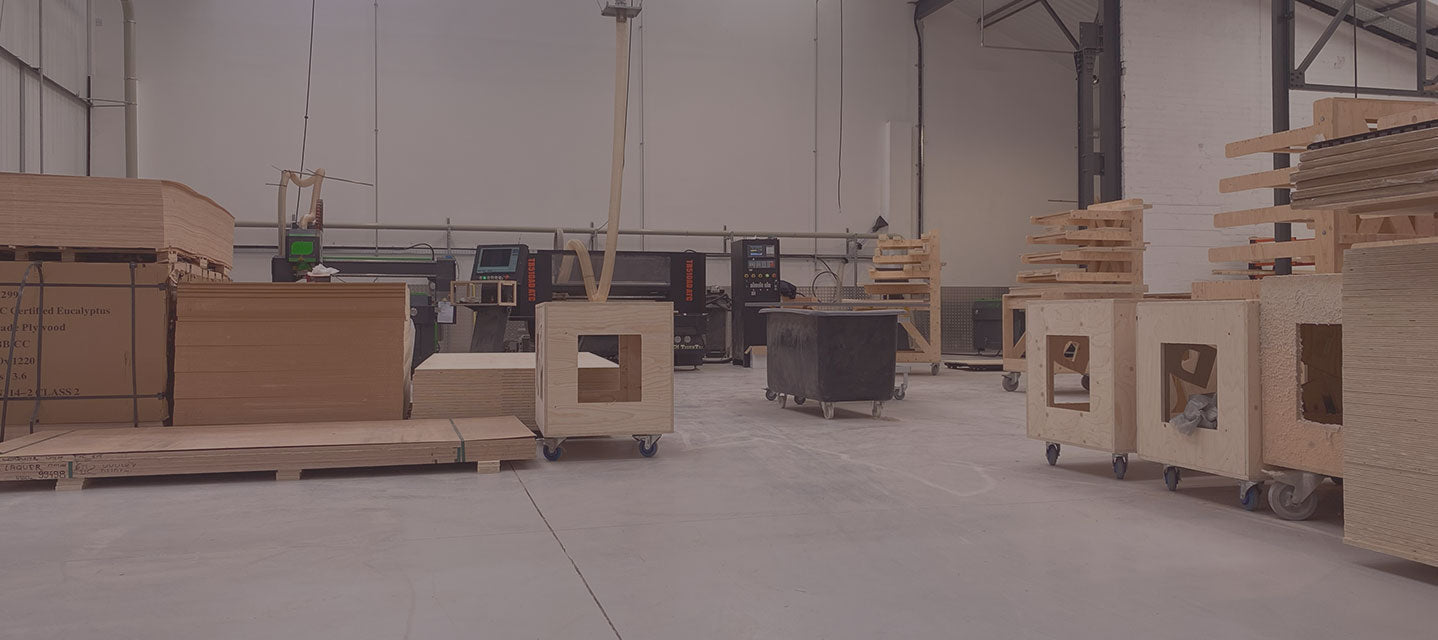
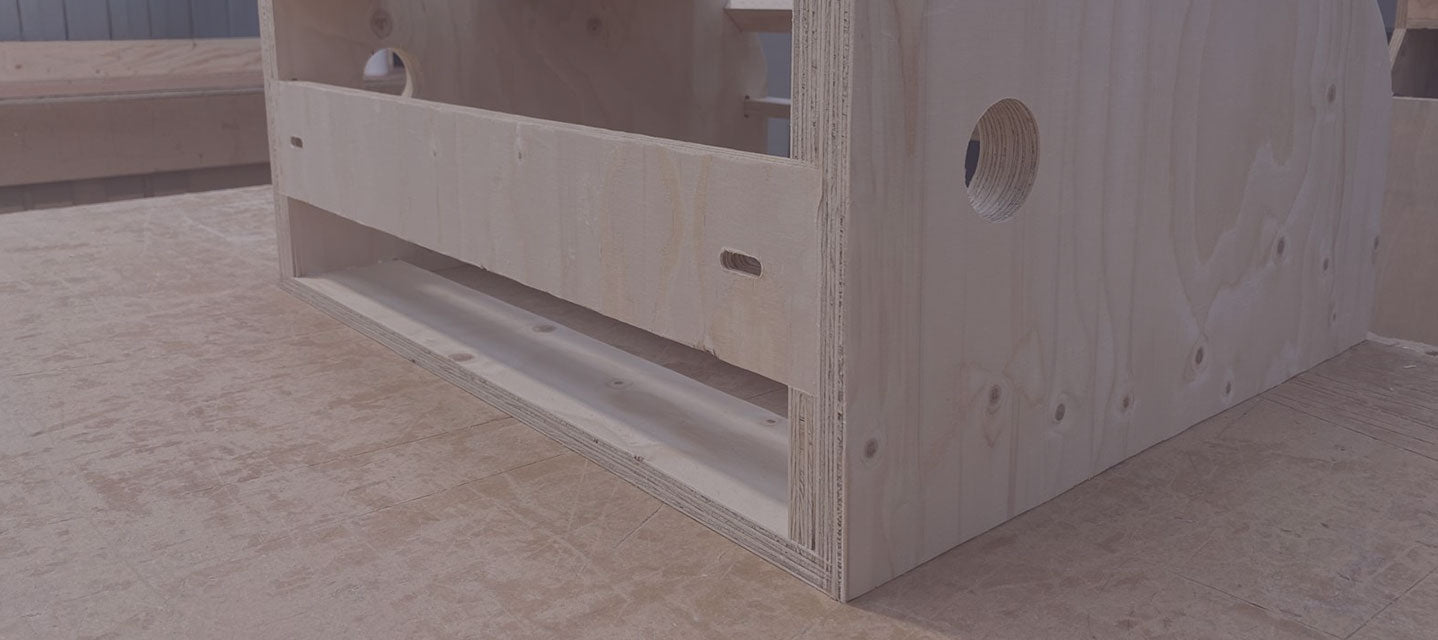
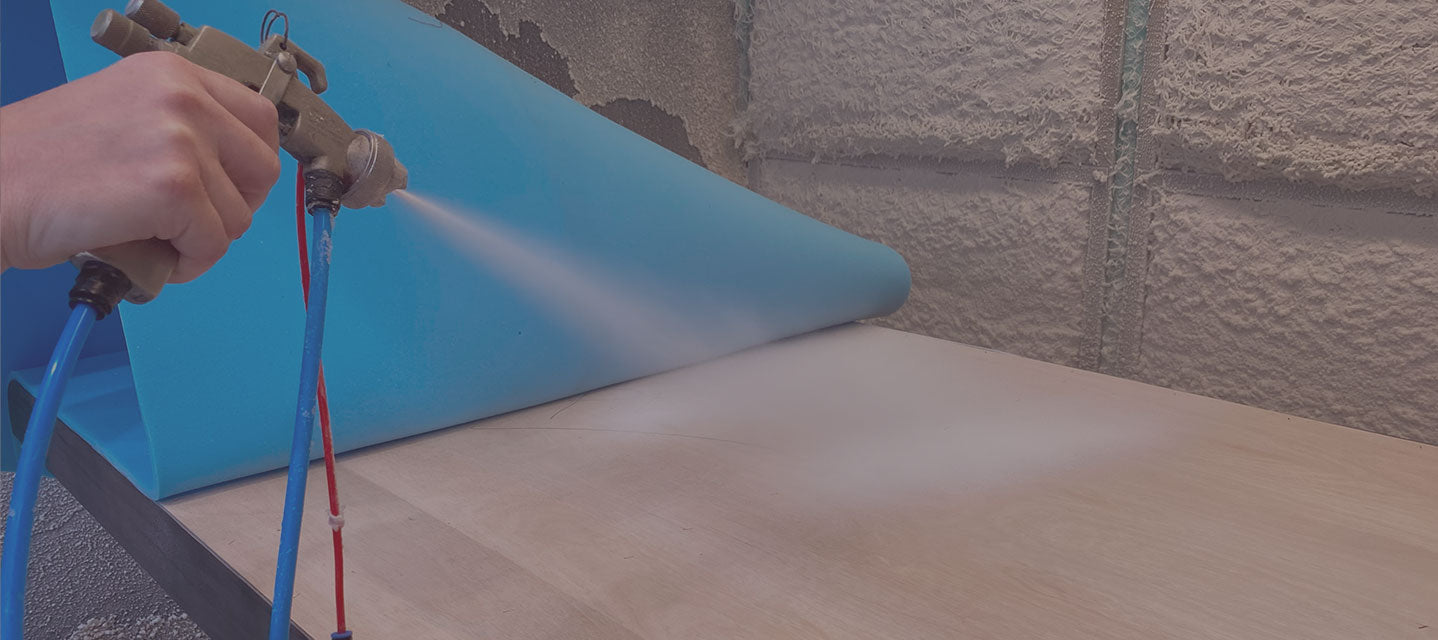
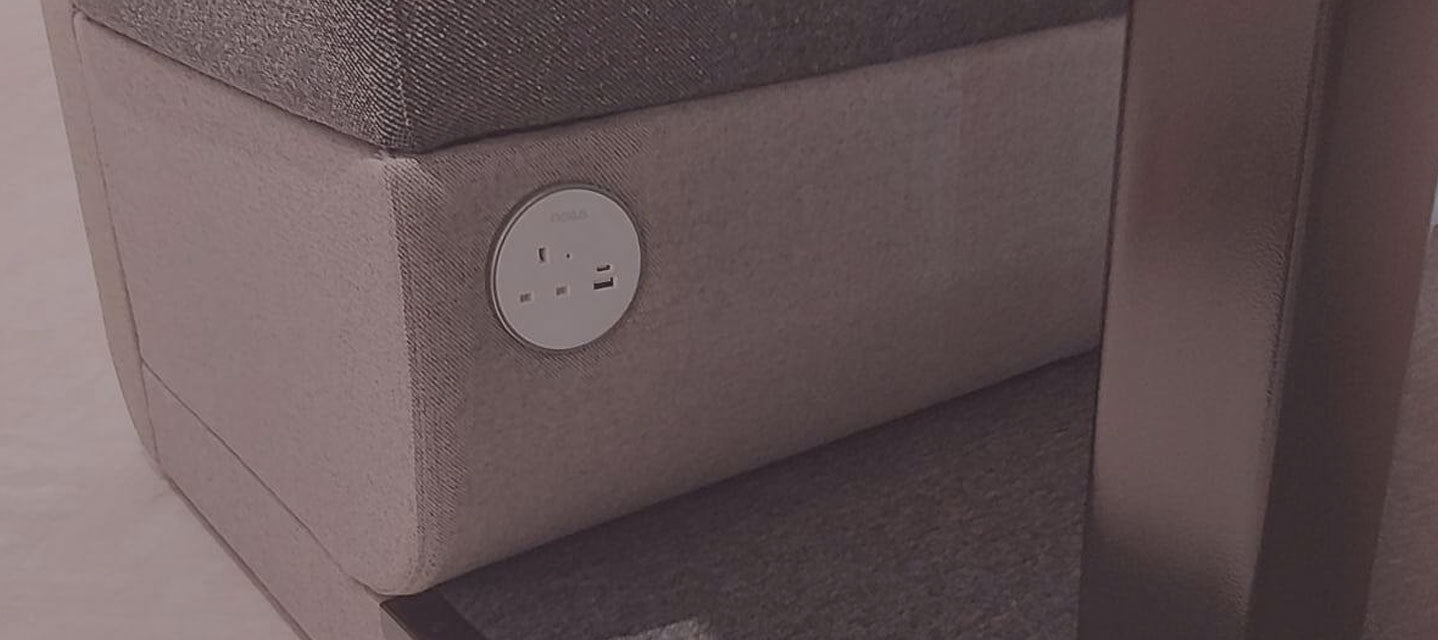
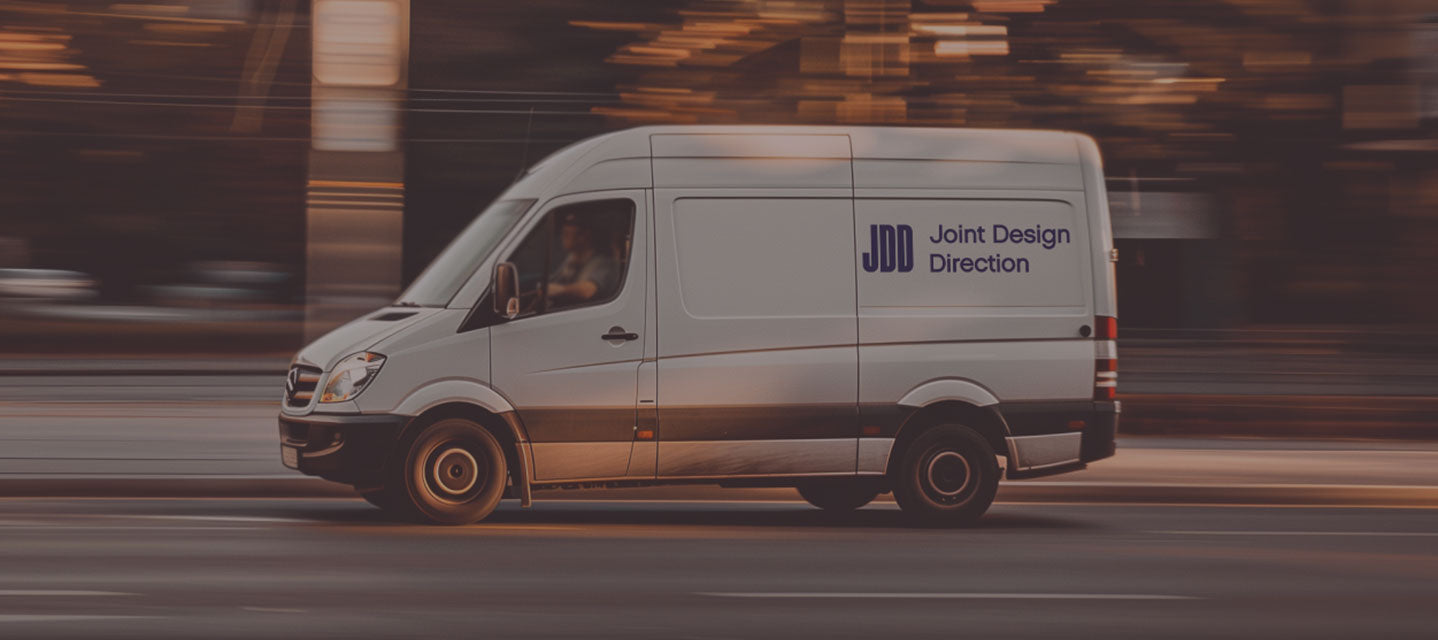
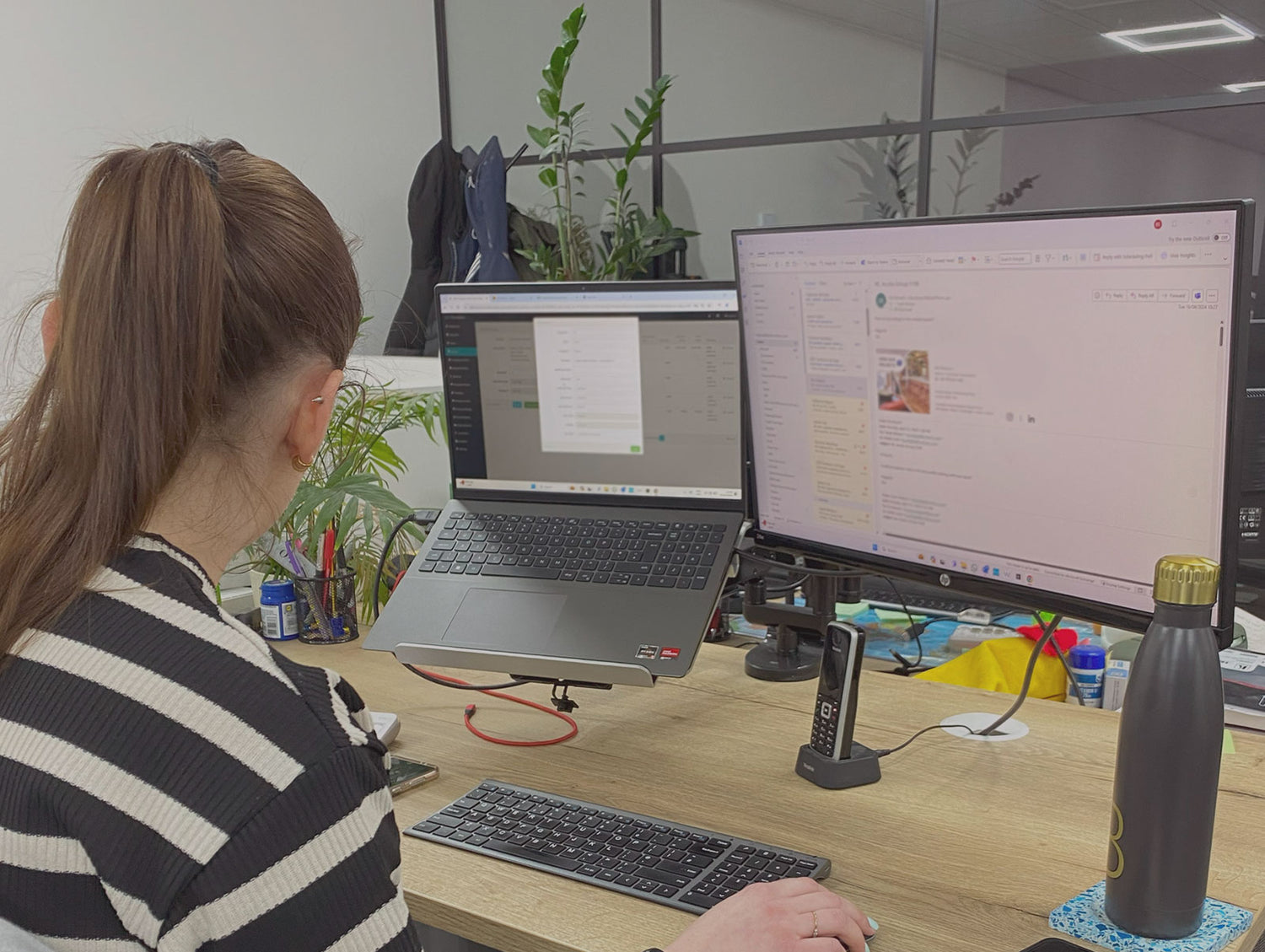
step 1
Understanding the specification
Working closely with you is pivotal to the success of any project. This collaborative approach lets us understand your needs, preferences, and objectives. By engaging with you, we develop a collaborative environment where ideas can freely flow and evolve.
Once we comprehensively understand your needs, we craft detailed product specifications. This specification is the blueprint for the entire project, outlining the products, fabrics, and technical requirements necessary to bring your vision to life.
Communicating with you at all times, we refine the specification, incorporating feedback and suggestions to ensure your satisfaction. The joint nature of our methods is about trust and transparency, enabling us to deliver innovative solutions that exceed expectations.

step 2
Order goes down to production
Once an order is received and deemed ready for production, our operational workflow kicks into gear to ensure seamless execution and timely delivery. Scheduling plays a crucial role in this process, enabling us to allocate resources efficiently while meeting expectations regarding lead time.
The scheduling process involves checking resource availability and order priority. By leveraging advanced scheduling techniques, we optimise our production timeline to minimise lead times while maintaining the highest standards of quality and efficiency.
With these systems in place, we are committed to delivering exceptional service and value. This streamlined workflow enhances operational efficiency and reinforces our reputation as a reliable and customer-centric partner in the manufacturing process.
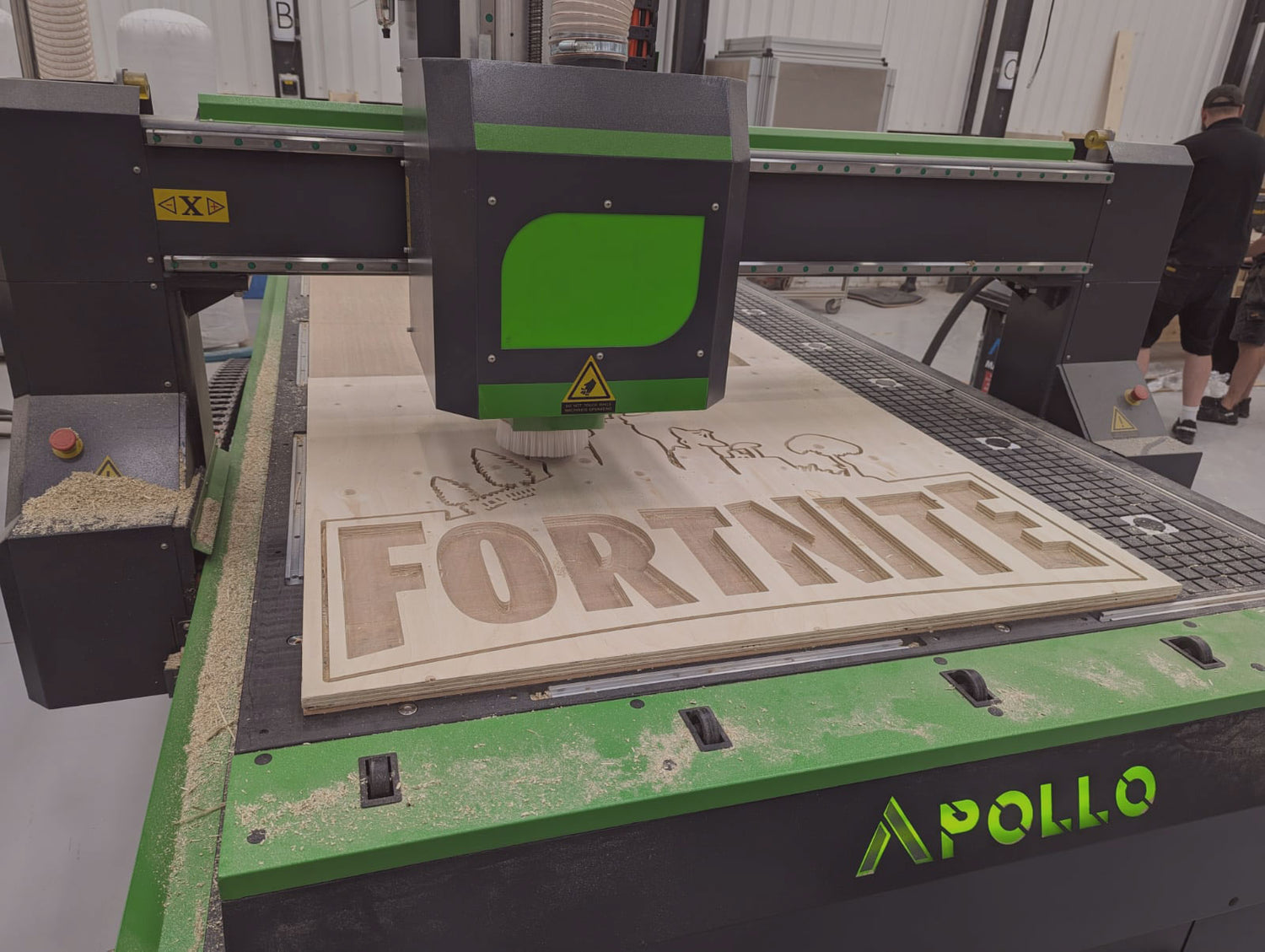
Step 3
Drawings are sent to the CNC machines
Our design engineers play a pivotal role in the precision manufacturing process, where attention to detail and expertise are paramount. Upon receiving the product drawings, our skilled engineers meticulously analyse every aspect to ensure it's correct before sending it to the factory floor – like one big Airfix model.
CNC production gives us an unparalleled level of accuracy and consistency. Programming our in-house CNC machines is a highly specialised task requiring technical proficiency and creative problem-solving. Our engineers leverage advanced software and cutting-edge technologies to generate intricate tool paths and commands that dictate the precise movements and operations of the CNC machines.
One of our core principles is sustainability, and this ethos extends to our manufacturing practices. We take extra care in placing each part within the raw material and optimising the layout to reduce timber waste and utilise more material.
Our commitment to sustainability goes beyond resource optimisation; it underscores our dedication to delivering value-driven designs that align with environmental stewardship and economic viability.
STEP 4
Quality check and hand-finished
After machining, the parts undergo a meticulous post-processing phase to ensure they meet our strict quality standards before assembly. This phase involves a combination of manual inspection, organisation, and finishing techniques to refine the parts and eliminate imperfections.
Our skilled technicians carefully inspect the cut parts to identify any irregularities or deviations from the specifications outlined in the product drawings. This manual inspection process allows us to detect even the slightest imperfections that may have occurred during machining.
Once inspected, the parts are organised systematically to streamline the subsequent assembly process. This ensures an efficient workflow and prevents any confusion or mix-ups, keeping the production schedule on track. Skilled craftsmen meticulously smooth out rough edges, remove burrs, and refine surfaces to achieve the desired aesthetic and functional quality. This manual refinement process not only enhances the visual appeal of the parts but also ensures that they meet the exacting standards expected from us.
Finally, detailed quality checks are conducted to verify the parts' dimensional accuracy, structural integrity, and overall quality.
The parts are deemed ready for assembly only after successfully passing these rigorous quality checks. This comprehensive approach to quality assurance underscores our commitment to delivering products of the highest calibre, known for precision, reliability, and impeccable craftsmanship.
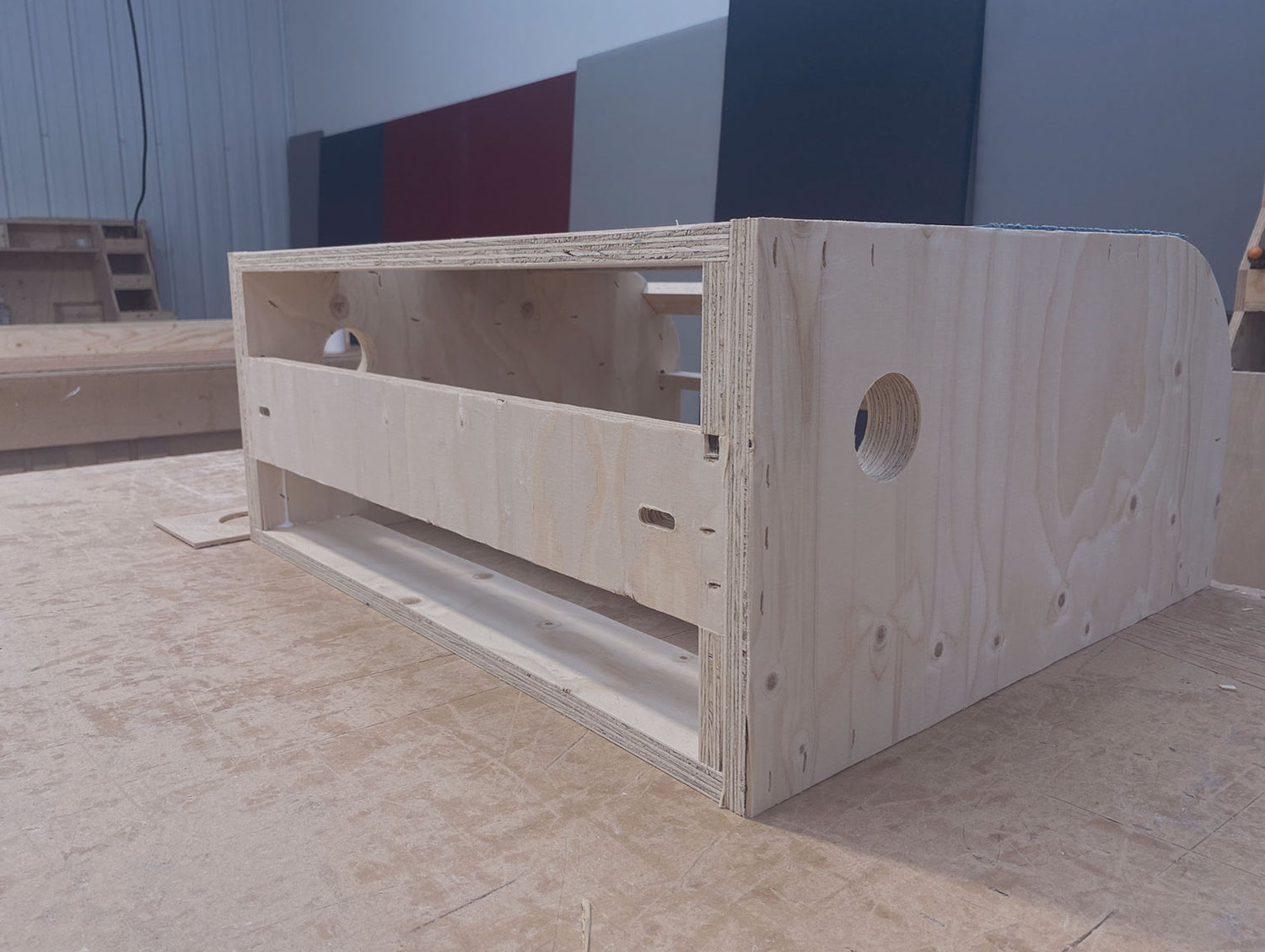
Step 5
Assembly
The assembly stage is where the product truly comes to life, as our highly trained in-house carpenters bring together the various 2D components to create the 3D forms that make up our products. With a keen eye for detail and a commitment to excellence, our carpenters approach each assembly task with precision and care, ensuring that every step is executed effectively and efficiently while upholding our uncompromising quality standards.
During the assembly process, attention is paid to every aspect of construction, from the alignment of individual parts to the joining techniques used. Our carpenters leverage their expertise and craftsmanship to achieve seamless integration and structural integrity.
Quality remains a top priority throughout the assembly process. Once the frame or structure is complete, it undergoes rigorous scrutiny and testing. This comprehensive testing regimen helps identify any potential weaknesses or deficiencies, allowing our team to address them proactively before the product progresses to the next stage of manufacture.
In essence, the assembly stage is where craftsmanship meets precision and quality meets excellence. Through the collective efforts of our skilled carpenters and stringent quality control measures, we strive to deliver products that exceed our expectations and yours, setting new benchmarks for quality and craftsmanship in the industry.
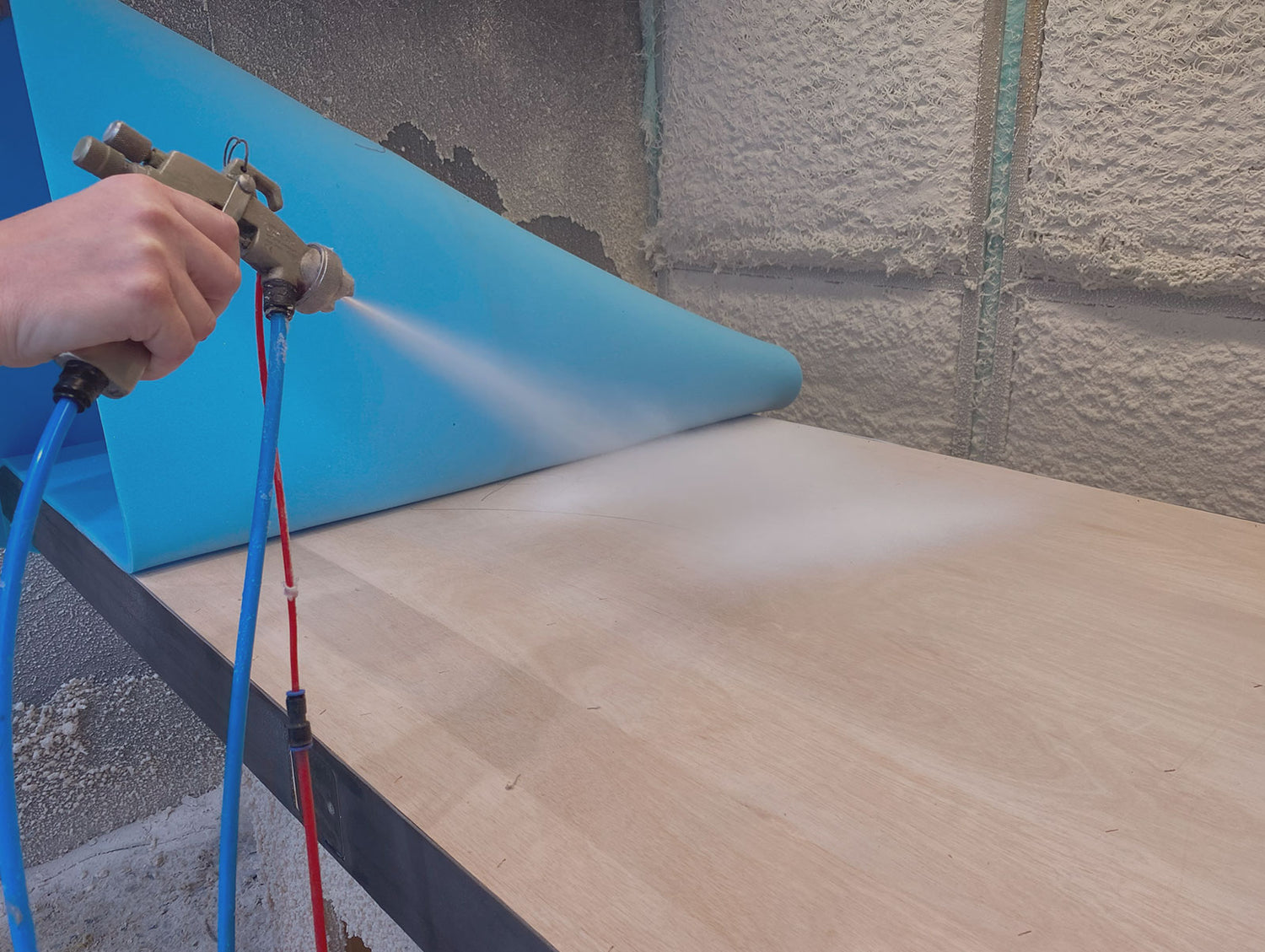
Step 6
The soft bit (foaming)
In our commitment to delivering products that excel in both comfort and safety, we employ a multi-layered foam application process to enhance the aesthetics and functionality of our furniture. Each foam piece is secured with a water-based spray glue.
Water-based spray glue isn't an industry standard. We are proud to include it in our manufacturing process because of its health benefits. Being low in VOC content, it is much more environmentally friendly, with fewer regulations and concerns, which makes it perfect for commercial products.
Let's talk about foam! We use several different foams, from high-density to soft and lightweight, to help create our overall look and feel.
The high-density foam provides cushioning and support, ensuring a plush and inviting feel that embodies the signature comfort our brand is renowned for. The thinner foam creates a soft touch texture that embodies the overall comfort JDD is known for. Finally, slim, dense foam creates clean, crisp edges and corners.
Investing in quality materials and innovative construction techniques ensures our products are of the highest quality.
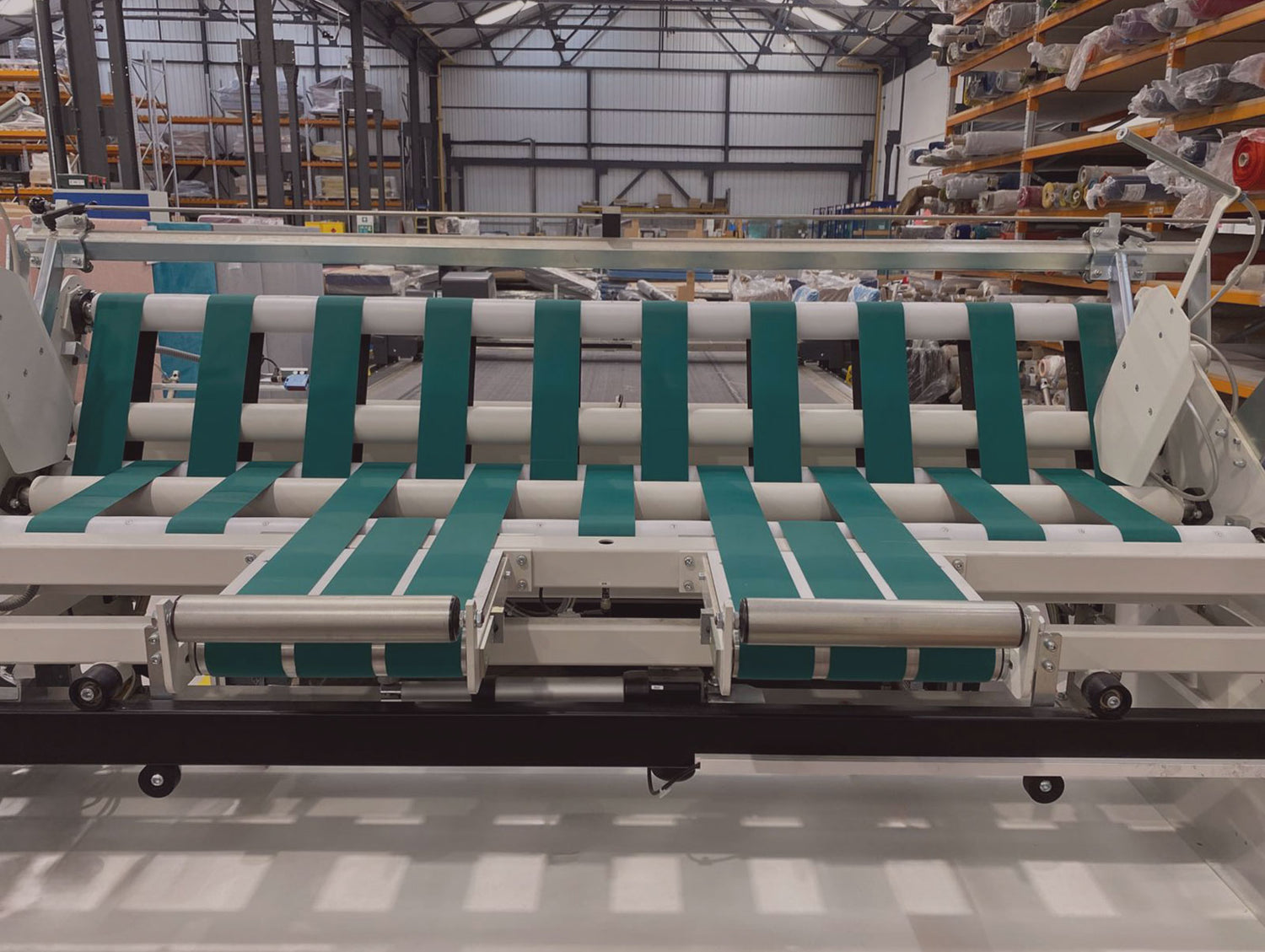
STEP 7
Sewing
In our commitment to delivering top-quality upholstered furniture, we leverage state-of-the-art technology and expert craftsmanship in our sewing process. Our premium cut Upholstery machine utilises CNC programming, is equipped with precision cutting technology, and efficiently cuts the fabric with unparalleled accuracy, saving valuable manual labour time and minimising material waste.
This advanced machine not only enhances productivity but also ensures consistency and precision in every cut, resulting in perfectly sized fabric pieces, pre-notched, that are ready for sewing. By automating the cutting process, we optimise efficiency without compromising on the quality of the final product.
Despite the efficiency of our cutting technology, we recognise the importance of human oversight in maintaining the highest standards of craftsmanship. Each fabric piece is inspected by hand to ensure there are no imperfections or errors that may have been missed during the automated cutting process.
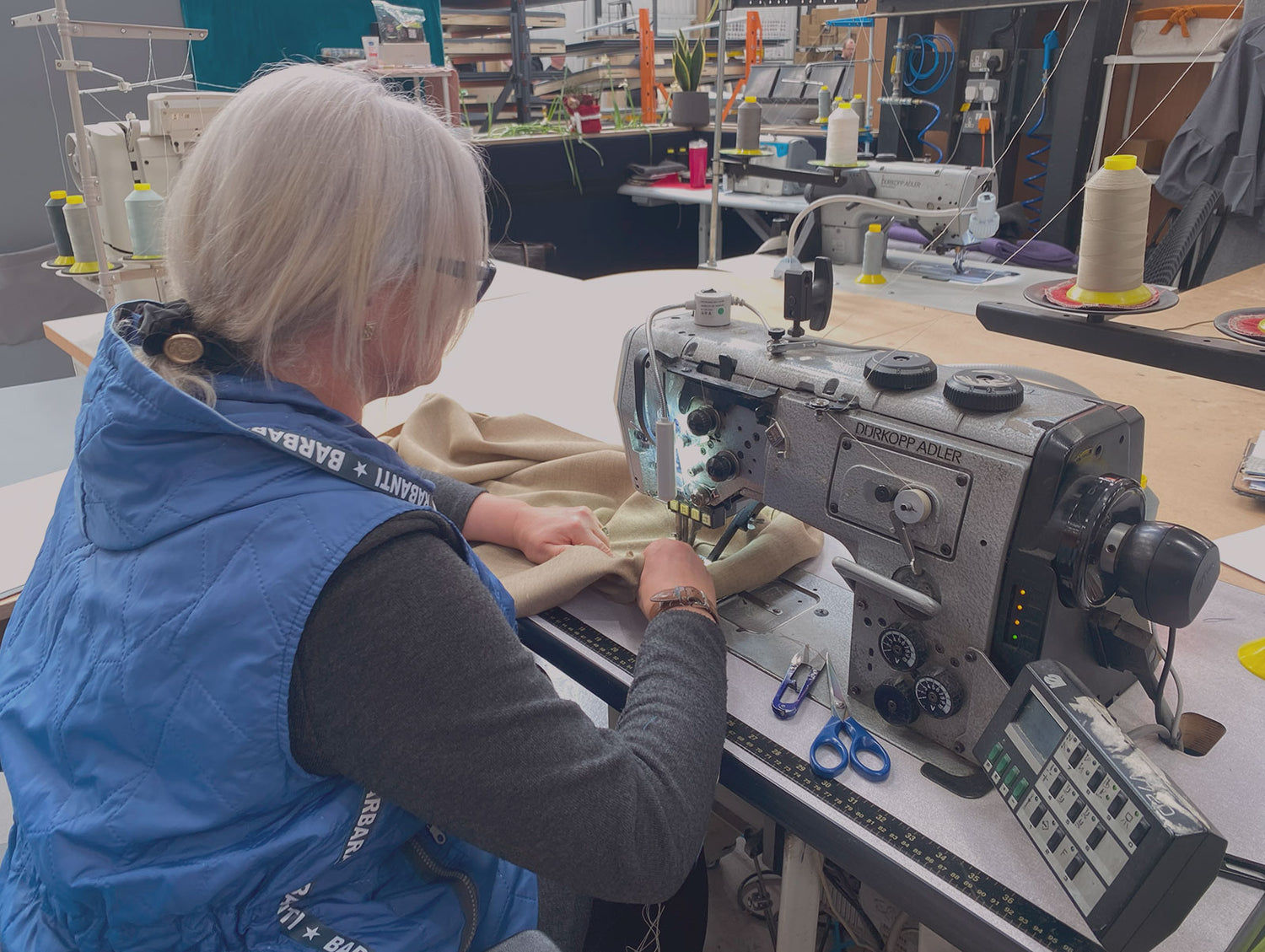
Our skilled sewers then take over, employing their expertise and attention to detail to hand-stitch the fabric pieces together, creating the fabric shell of the furniture piece. This manual stitching process not only ensures precision and durability but also allows for customisation and intricate detailing, catering to each piece's unique specifications and design requirements.
This perfect blend of artistry and machine allows us to balance efficiency and quality, delivering upholstered furniture that embodies luxury, comfort, and durability. Our commitment to excellence permeates every step of the sewing process, resulting in products that exceed expectations and stand the test of time.
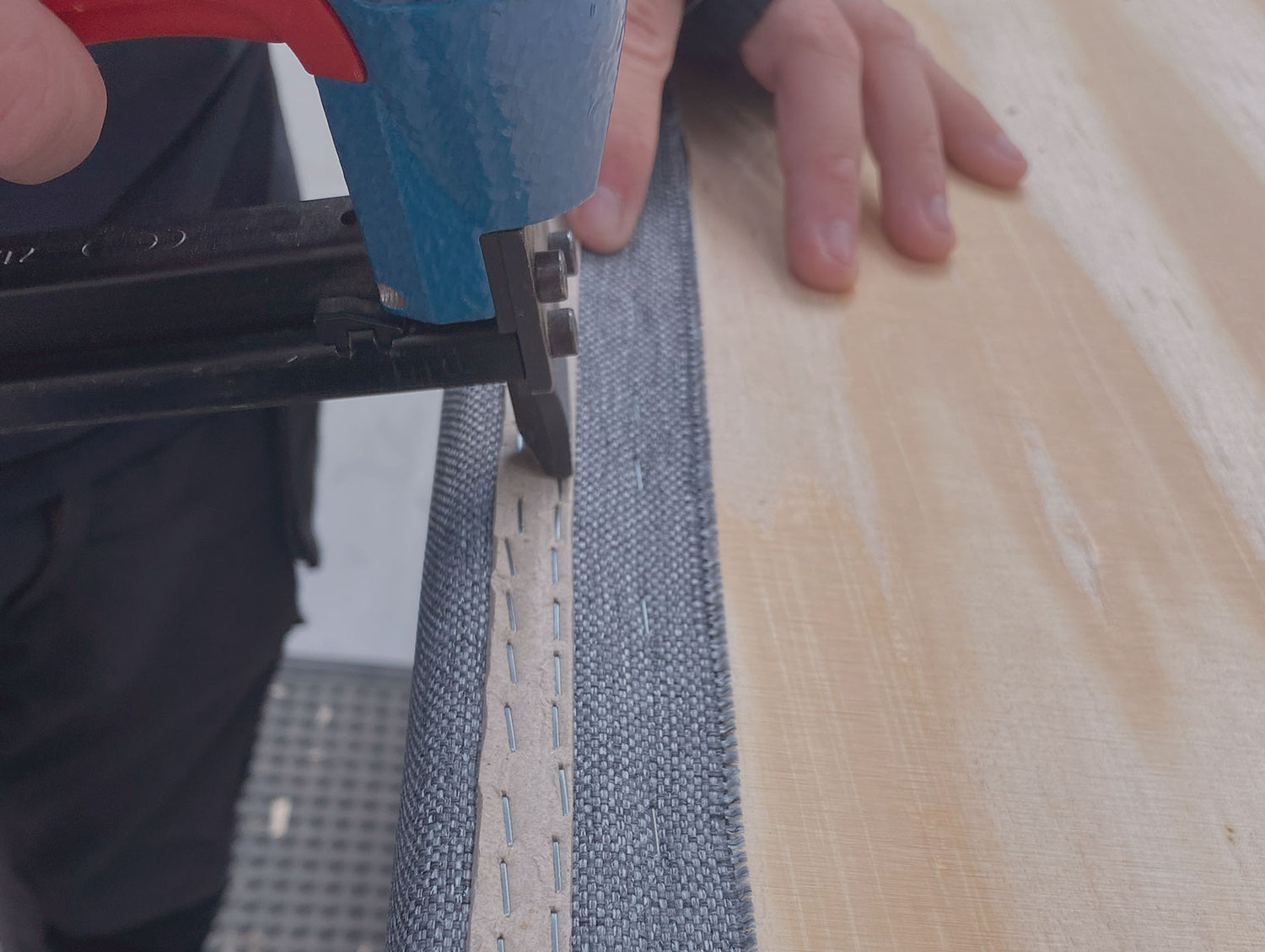
Step 8
Upholstery
With the fabric shell complete, our skilled upholsterers now undertake the critical task of tailoring it onto the foamed timber frame. They execute this step with precision and care using various hand tools, ensuring the fabric is perfectly positioned and securely fastened while achieving a flawless, smooth finish.
Investing in the best tools and techniques allows our upholsterers to work swiftly and efficiently, minimising production time. The high-powered staples penetrate the fabric and securely anchor it to the timber frame, providing a strong foundation for the upholstered furniture.
Throughout the stapling process, our upholsterers pay close attention to detail, adjusting the tension of the fabric to ensure a snug and wrinkle-free fit. Achieving the perfect tension is crucial not only for aesthetic purposes but also for the product's longevity. Properly secured fabric prevents sagging, shifting, and premature wear, ensuring the furniture maintains its pristine appearance and structural integrity over time.
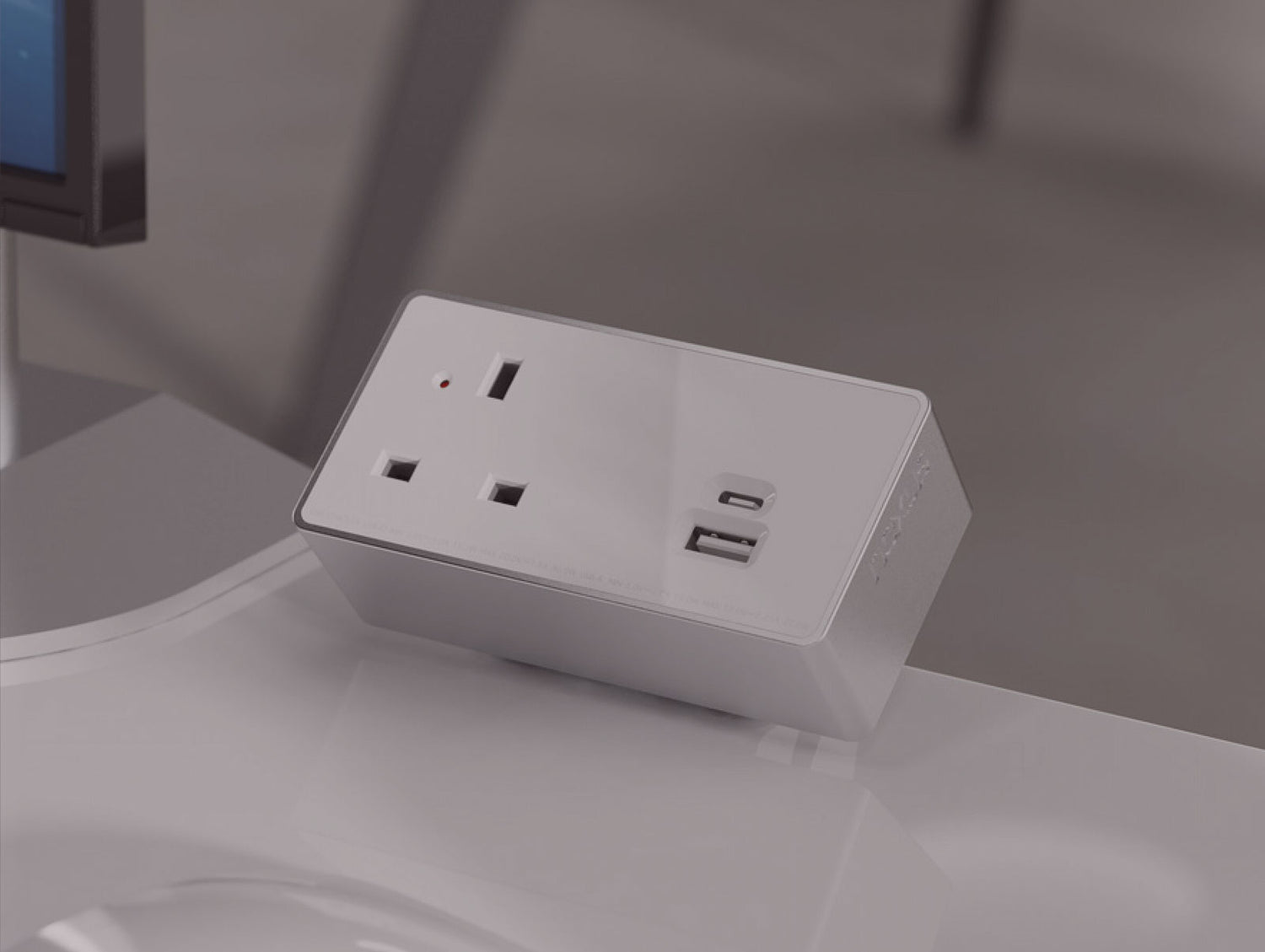
Step 9
Components & Electrics
For products that require power, we have a team of electricians who can add all the functionality and smart technology you could want. Details matter to us, so all cable runs are kept hidden by being cut into the products at the CNC stage. This means the aesthetics aren't impacted.
Ventilation is important in our meeting pods and roofed dens. To provide comfort for the user and a constant flow of fresh air, we use a system to cycle the air regularly. We have put a lot of work into ensuring this system is as quiet as possible.
Automatic PIR sensors ensure that the LED lights come on automatically when entering the pod and turn themselves off when you leave. This saves energy and helps reduce everyone's carbon footprint. If it's too bright or cold while in our pods, the wall-mounted dimmer switches allow you to control the ambient lighting and fan speed to suit your needs.
We can also add power sockets to our furniture as required. Choose from UK sockets, USBA, USBC and data, amongst others. For placement, we can install them on the table, under the table or in the seat, depending on the product and your requirements.
STEP 10
Quality Control
At our facility, quality control isn't just a step in the process—it's a cornerstone of our commitment to providing good, honest products. Once our products are completed, they undergo a rigorous quality control check to ensure that every detail meets our exacting standards before leaving our headquarters.
Our quality control process leaves no stone unturned. Every inch of the product is examined for imperfections, ensuring that it meets the highest standards of craftsmanship. In addition to inspecting the physical aspects of the product, we also conduct thorough checks on any electrical components. Each electrical component is checked to ensure that it meets safety standards and functions reliably.
We understand that even the smallest flaw can detract from our product's overall quality and satisfaction. That's why we're committed to delivering only the finest goods to our customers. We hold ourselves to the highest standards and refuse to accept anything less than excellence. When you choose our products, you can rest assured that they've undergone the most stringent quality control checks.
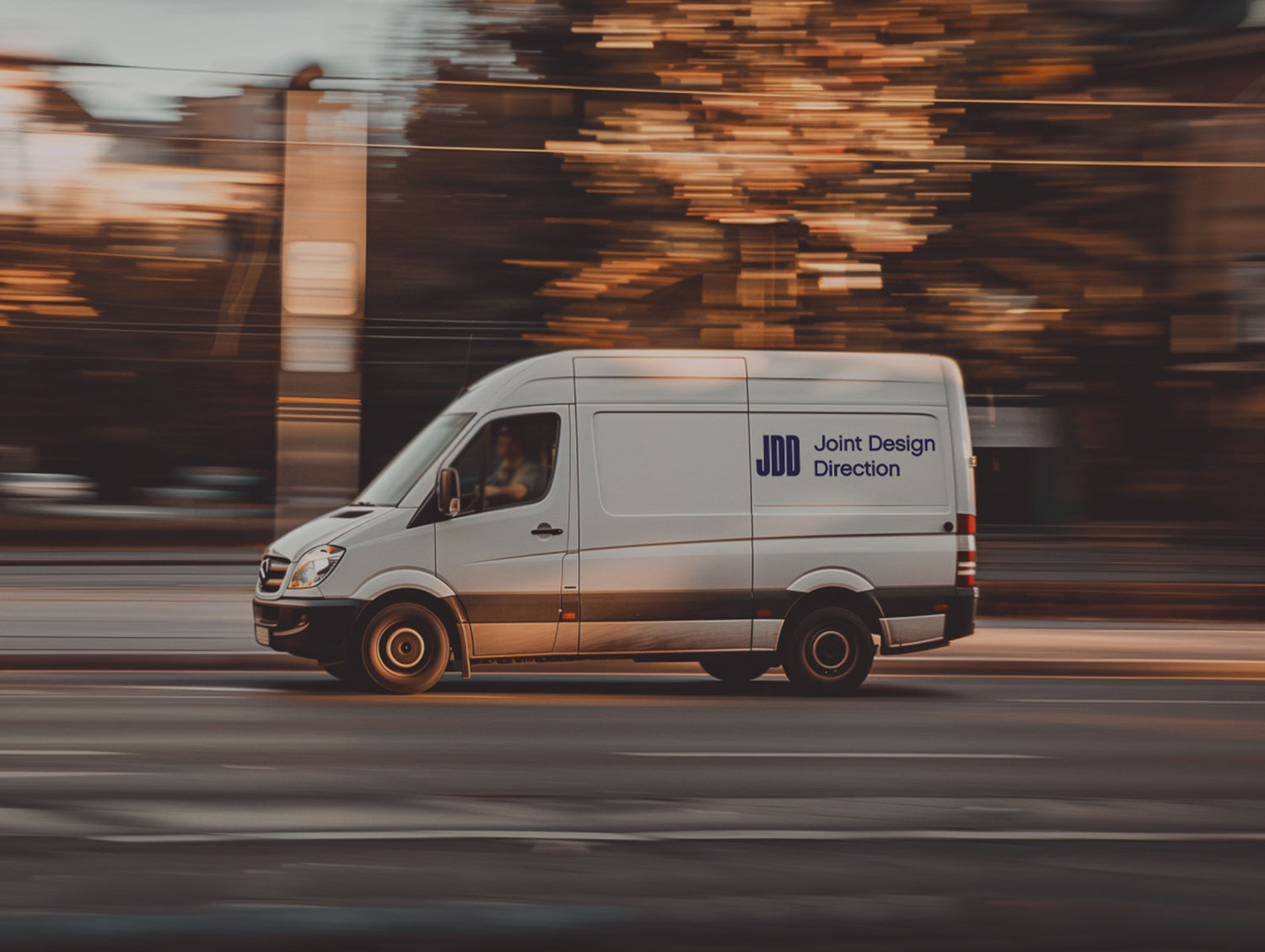
Step 11
Packaged & Shipped
Our dispatch team understands the importance of handling each product with the utmost care and attention. They begin by carefully dismantling the product, ensuring that each component is handled carefully to avoid damage.
Our team then wraps each component using high-quality materials specifically chosen to provide maximum protection during transit. We spare no expense in ensuring that your product arrives in pristine condition.
Our commitment to perfection doesn't end until your product has been safely delivered and installed in your business. From start to finish, we take pride in delivering a seamless and exceptional experience, ensuring that your satisfaction remains our top priority every step of the way.
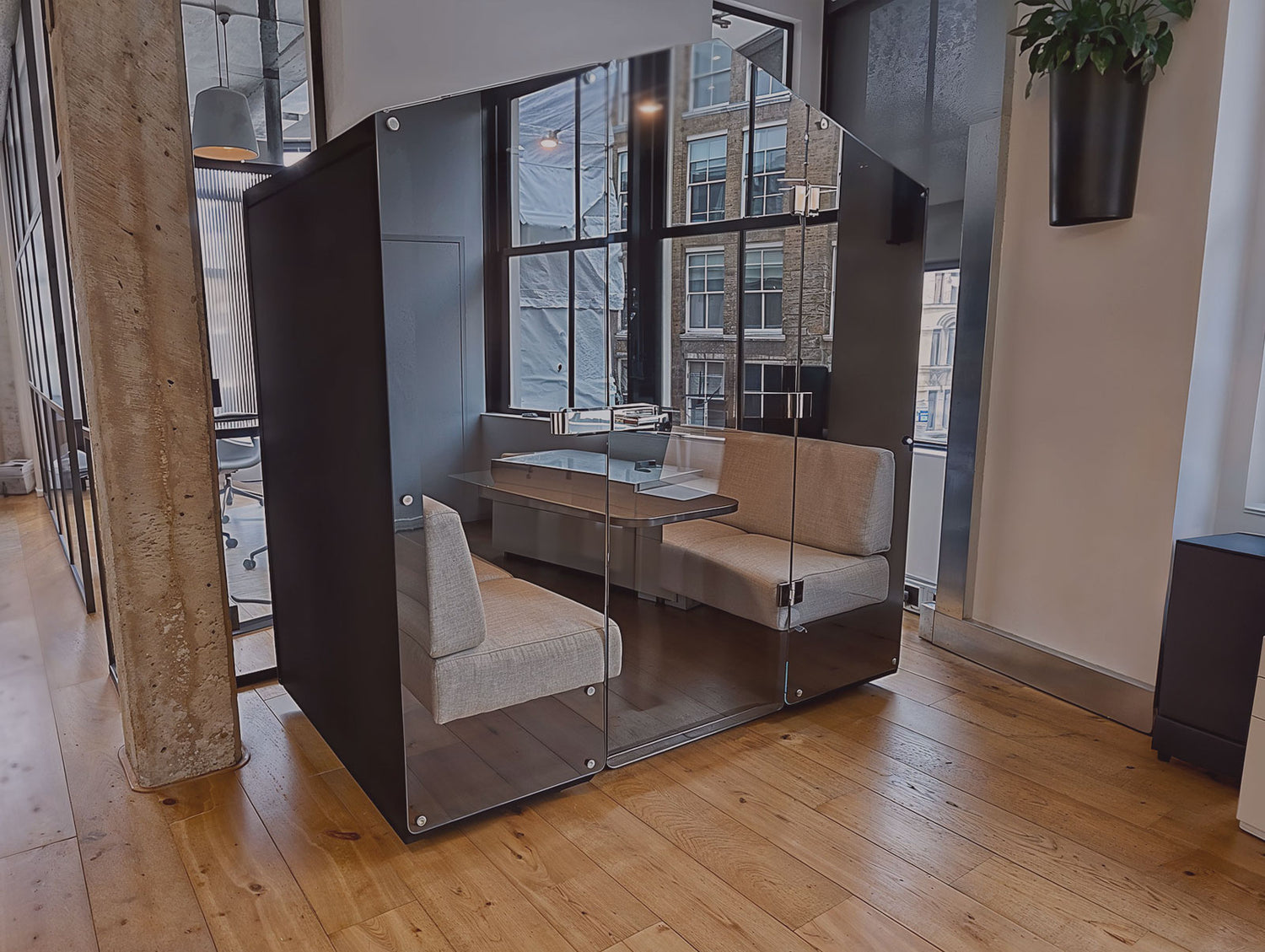
Step 12
Delivery & Installation
At JDD Furniture, we understand that the delivery and installation process is a crucial final step in ensuring your complete satisfaction with our products. That's why we've invested in a fleet of vehicles and established a dedicated team of in-house drivers and fitters committed to providing a seamless and hassle-free experience from start to finish.
Once your product is ready for delivery, our experienced installation teams will collect it from our headquarters and transport it to your desired location anywhere in the UK. Upon arrival, you will be warmly greeted by our friendly and professional team, who will carefully unload the product from our vehicle.
Following your previously agreed-upon instructions, our skilled fitters will assemble and install the products according to your specifications. Throughout the installation process, we conduct on-site quality checks to verify that everything meets our high standards of excellence. Our goal is to exceed your expectations, so we take every precaution to ensure that the result is perfect.
Our team will consider the job complete only once you are completely satisfied with the installation. We understand the importance of your time and the significance of getting everything right, so we're committed to staying until you're happy with the results.
step 13
Follow Up
We believe in building long-lasting customer relationships beyond completing a single job. We understand that your satisfaction and peace of mind are paramount, so our care and support doesn't end once the installation is complete.
After you've had time to familiarise yourself with your new products and settle into your space, we are still only a phone call away. Our dedicated customer care team will be available to follow up on your experience and address any questions or concerns you may have.
We take pride in our ability to provide honest, personalised support and assistance tailored to your needs. Whether you have questions about your new products' functionality, need additional maintenance and care guidance, or simply want to share feedback, we're here to listen and provide solutions.
In addition to follow-up care, we offer in-person chats if you prefer a more hands-on approach. Our sales team is happy to schedule a convenient time to meet with you in person, allowing us to address any questions or queries face-to-face.
Our company's heart is a commitment to excellence and customer satisfaction. We believe great relationships are built on trust, communication, and genuine care. That's why we go above and beyond to ensure that your experience with us is positive and memorable.